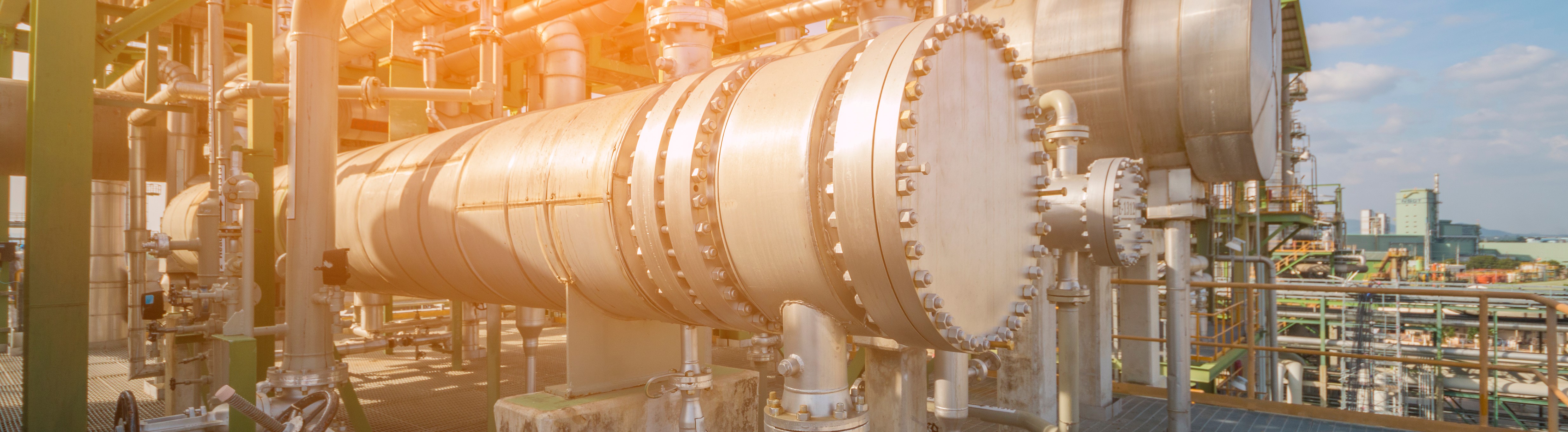
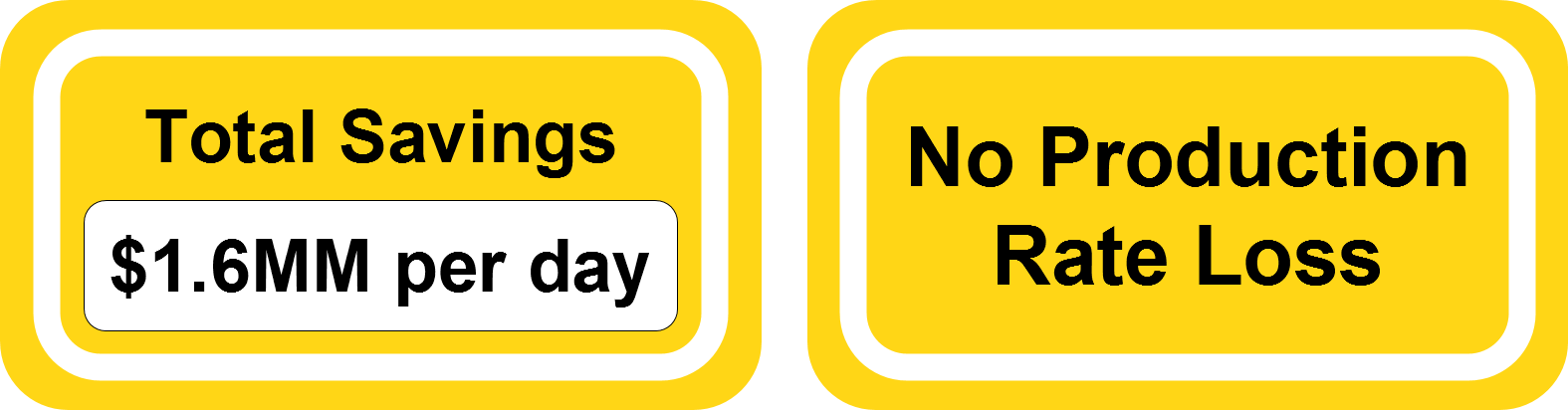
Una planta mejoradora de crudo canadiense corría el riesgo de que se viera afectada la capacidad de procesamiento de agua ácida en todo el sitio por la tendencia a la formación de espuma que se registraba en la sección superior de la torre del concentrador. Estos episodios de generación de espuma variaban considerablemente, en general según la contaminación del agua ácida del coquizador en las etapas iniciales del proceso, y podían causar dificultades operativas.
Como no se contaba con un tratamiento para los casos en que se producían estas situaciones, la única opción era reducir considerablemente la carga del coquizador en las fases iniciales. Antes, un único episodio de formación de espuma exigía disminuir la tasa de procesamiento en el coquizador en un 42%, lo que disminuía la producción hasta en 50 KBPD (figura 2). Este episodio duraba 30 días y le costaba a la planta $48 millones, o $1.6 millones por día.
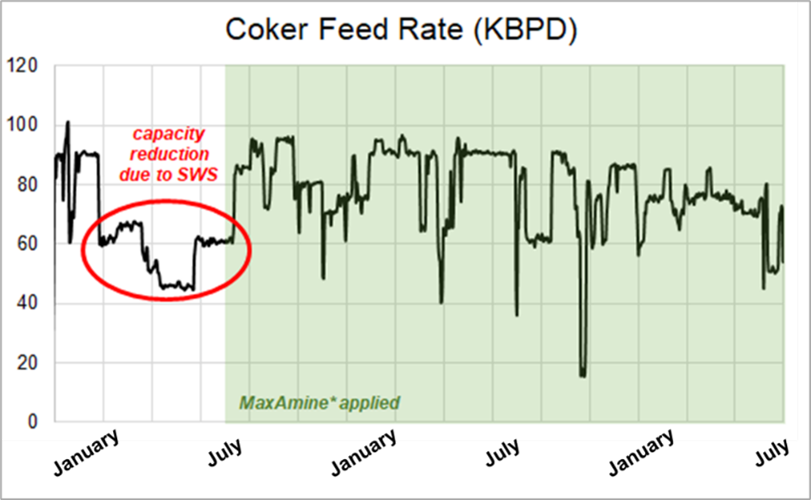
Figura 1. La tasa de alimentación del coquizador, diseñado para una capacidad de 95 KBPD, se había reducido un 42% debido a la formación de espuma.
El objetivo de la torre del concentrador de agua ácida es eliminar el amoniaco y el sulfuro de hidrógeno (H2S) de las corrientes de agua ácida generadas en toda la planta. La torre del concentrador genera un agua ácida depurada que puede reciclarse y volver a incorporarse al proceso, así como una corriente de residuos líquidos concentrados.
Los hidrocarburos aromáticos, como la nafta, pueden ser una fuente importante de contaminación en la corriente de agua ácida de entrada del concentrador, lo que genera espuma en el interior de la torre. La espuma actúa como "portador" físico, lo que provoca que se desborde el líquido en el acumulador superior del concentrador y, por lo tanto, se limite la tasa de procesamiento general de la materia prima del coquizador.
En esta planta mejoradora, se detectó que el agua ácida del proceso de coquización estaba contaminada regularmente con hidrocarburos aromáticos, lo que generaba episodios importantes de formación de espuma y desborde excesivo de líquido. El equipo de ingeniería de la planta colaboró estrechamente con Veolia para analizar el problema de la espuma y encontrar una solución que mitigara el riesgo de desbordamiento de líquido y disminución del rendimiento del coquizador.
Max-Amine, un producto antiespumante específico para hidrocarburos, fue considerado la mejor opción, ya que constituía una solución química en línea fácil de usar que permitiría mitigar los episodios variables de formación de espuma en el concentrador de agua ácida sin tener que disminuir la tasa de procesamiento del coquizador.
Resultado
El producto demostró gran eficacia para reducir la formación de espuma en la torre del concentrador y posibilitó la flexibilidad necesaria para que el coquizador de la planta mejoradora funcionara a su máxima capacidad de procesamiento.
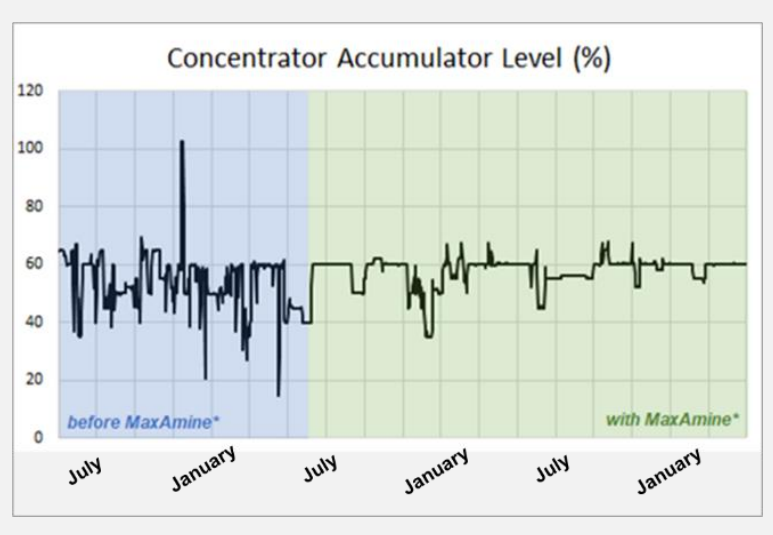
Figura 2. Nivel en el acumulador superior del concentrador antes y después de la inyección de Max-Amine.
Veolia siguió manteniendo un excelente trabajo de cooperación con el equipo de Operaciones de la planta a medida que la aplicación de Max-Amine iba estabilizando el agua ácida al nivel de inventario y lograba evitar la reducción de la tasa de procesamiento de un coquizador. Esto evitó que se produjera otro episodio de interrupción similar al anterior, que había generado pérdidas de $48 millones en 30 días, o $1.6 millones por día.
En síntesis, la aplicación del antiespumante Max-Amine contribuyó a evitar tiempos de inactividad en la producción y la necesidad de desviar los volúmenes de los tanques de agua ácida. En cuanto a los beneficios financieros, se estimó que la aplicación de antiespumante le permitió al cliente ahorrar $1.6 millones por día al evitar la pérdida de producción.