Planta Frederickson Power - Tacoma, Washington
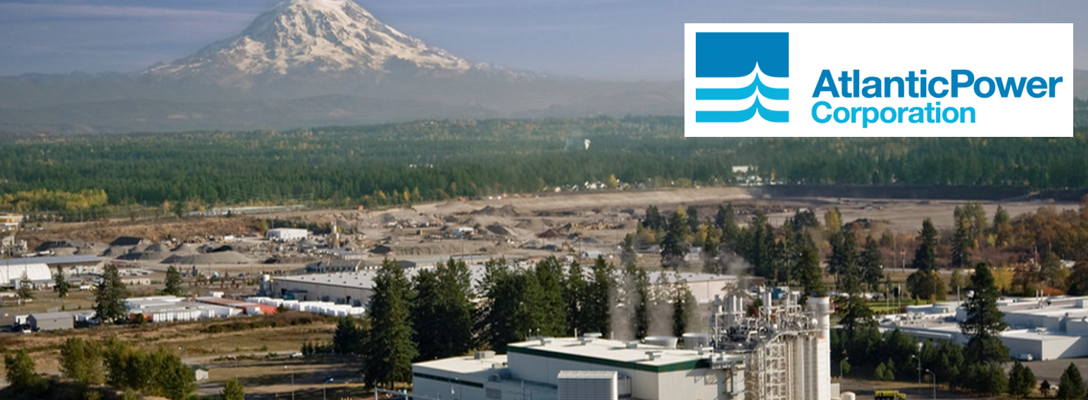
Muchas plantas de energía operan con un modo de entrega a pedido, abasteciendo a la red con un día de antelación por unos pocos días o unas pocas semanas a la vez. Desafortunadamente, este modo de operación implica que el sistema de generación de vapor se activa y se desactiva de forma regular, lo que expone a activos críticos a condiciones difíciles como la intrusión de aire y una química inestable del agua.
Los generadores de vapor cíclicos son especialmente susceptibles al ataque de oxígeno, la corrosión por pH ácido y la corrosión por flujo (flow-assisted corrosion, FAC). Estos inducen corrosión en todo el sistema, lo que tiene un impacto severo en la confiabilidad de la planta y representa un alto costo de mantenimiento.
Desafío
Frederickson Power es una planta de energía de ciclo combinado de 250 MW y que es operada por Atlantic Power en el estado de Washington. Su sistema de generación está compuesto por una turbina de gas que envía los gases de combustión a un generador de vapor de recuperación de calor (heat recovery steam generator, HRSG) de 3 tambores, que impulsa una turbina de vapor.
El tambor de baja presión (low pressure, LP) proporciona agua de alimentación a los tambores de presión intermedia (intermediate pressure, IP) y de alta presión (high pressure, HP), y la purga del tambor de HP cae en cascada al de IP. El programa de tratamiento de agua de caldera incluye fosfato (PO4) alimentado al tambor de HP y una mezcla de amoníaco/etanolamina para el tratamiento de condensado de vapor.
La planta tiene un promedio de 12 arranques en frío por año y puede funcionar desde unas pocas horas hasta algunas semanas cada vez. El principal desafío de la planta es el tiempo de inactividad entre cada ejecución, que puede durar hasta un par de meses.
La imagen 1 muestra que se observaron altos niveles de hierro en el arranque del sistema de caldera durante muchos días, especialmente en los tambores de IP y HP, lo que indica que se estaba produciendo una severa corrosión fuera de línea. El procedimiento de parada de la planta incluyó la protección con nitrógeno, pero el sistema no se pudo drenar ya que se requería que estuviera disponible para comenzar con un día de anticipación.
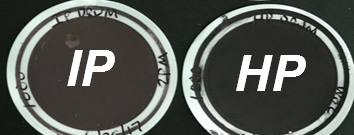
Imagen 1: Antes de la poliamina: las muestras de Millipore de hierro del tambor después de dos días de funcionamiento presentan >10 ppm de hierro
La pérdida de metal base debido a FAC también se confirmó en el evaporador de LP mediante inspecciones por ultrasonido (ultrasonic testing, UT). En función de las lecturas de espesor de las UT, Frederickson Power reparaba muchos tubos cada año.
Solución
Para mitigar los problemas de corrosión fuera de línea y FAC en su sistema de caldera, Atlantic Power quería considerar el uso de un tratamiento de formación de película volátil de vapor. Veolia recomendó el uso de su tecnología de poliaminas además de los productos químicos actuales para el tratamiento del agua de caldera. La poliamina es una tecnología de película volátil única que puede proporcionar una fuerte protección contra la corrosión en línea y fuera de línea de los sistemas de caldera, tanto en la fase de agua como de vapor.
La primera fase de la prueba fue un período de funcionamiento de 55 días en el que se aplicó poliamina continuamente al agua de alimentación de la caldera. Luego, la planta dejó de funcionar durante 70 días. En la siguiente puesta en marcha, se observó una reducción de los niveles de hierro, aunque todavía eran altos, especialmente en las áreas más afectadas de los tambores de IP y HP.
La segunda fase de la prueba consistió en 87 días de tratamiento continuo con poliamina. Nuevamente, no se cambiaron los parámetros operativos ni de parada de la primera prueba ni las prácticas operativas históricas. La siguiente parada duró 66 días, y cuando la planta volvió a estar en línea, se pudo observar una reducción drástica de hierro en todas las secciones del sistema.
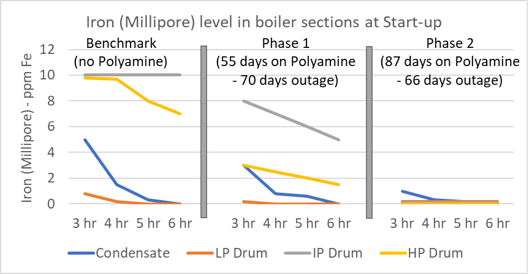
Imagen 2: Nivel de hierro (Millipore) en las secciones de la caldera en la puesta en marcha (entre 3 y 6 horas después de la puesta en marcha)
La figura 1 muestra la progresión del hierro en los tambores de condensado, de LP, IP y HP antes de la prueba inicial y durante las fases 1 y 2 de la prueba.
Resultado
Después de un total de 142 días de aplicación de poliamina (fases 1 y 2), no se observó en la planta ningún nivel de hierro en ninguno de los tambores 3 horas después de la puesta en marcha. Esto indica que la poliamina mitigó con éxito la corrosión en todas las áreas del sistema de caldera y de vapor. Las imágenes 2 y 3 muestran que después de un total de 142 días de aplicación de poliamina (fases 1 y 2), no se observó en la planta ningún nivel de hierro en ninguno de los tambores 3 horas después de la puesta en marcha. Esto indica que la poliamina mitigó con éxito la corrosión en todas las áreas del sistema de caldera y de vapor. Las imágenes 2 y 3 muestran la progresión desde el punto de referencia hasta las fases 1 y 2 de la prueba a las 3 horas después de la puesta en marcha para los tambores de IP y HP.
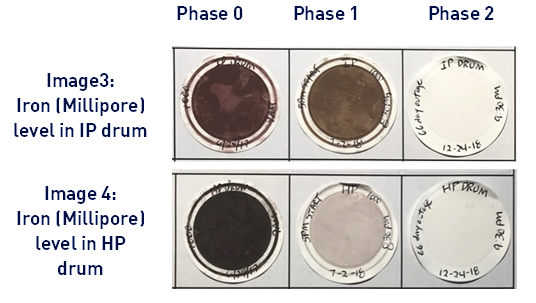
El beneficio del nuevo tratamiento con poliaminas tiene un impacto positivo en la operación y confiabilidad de la planta, como afirmó Joe Brooks, jefe de operaciones y mantenimiento en la Planta Frederickson Power:
"Desde que implementamos el tratamiento con poliaminas, la tasa de FAC se ha reducido notablemente".
Joe Brooks, jefe de operaciones y mantenimiento
Las siguientes imágenes fueron tomadas durante una inspección reciente después de estar fuera de línea durante 66 días. Las superficies hidrofóbicas se observan en todo el sistema, incluidas las áreas de la fase de vapor, y no hubo corrosión a pesar de que el sistema se dejó lleno de agua durante las paradas.
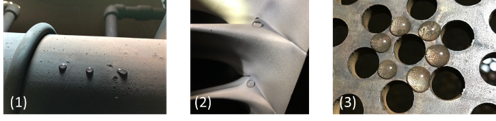
Imagen 5: Superficies hidrofóbicas en el tambor de HP (1), álabes de la turbina de vapor (2) y filtro del pozo de condensado (3)