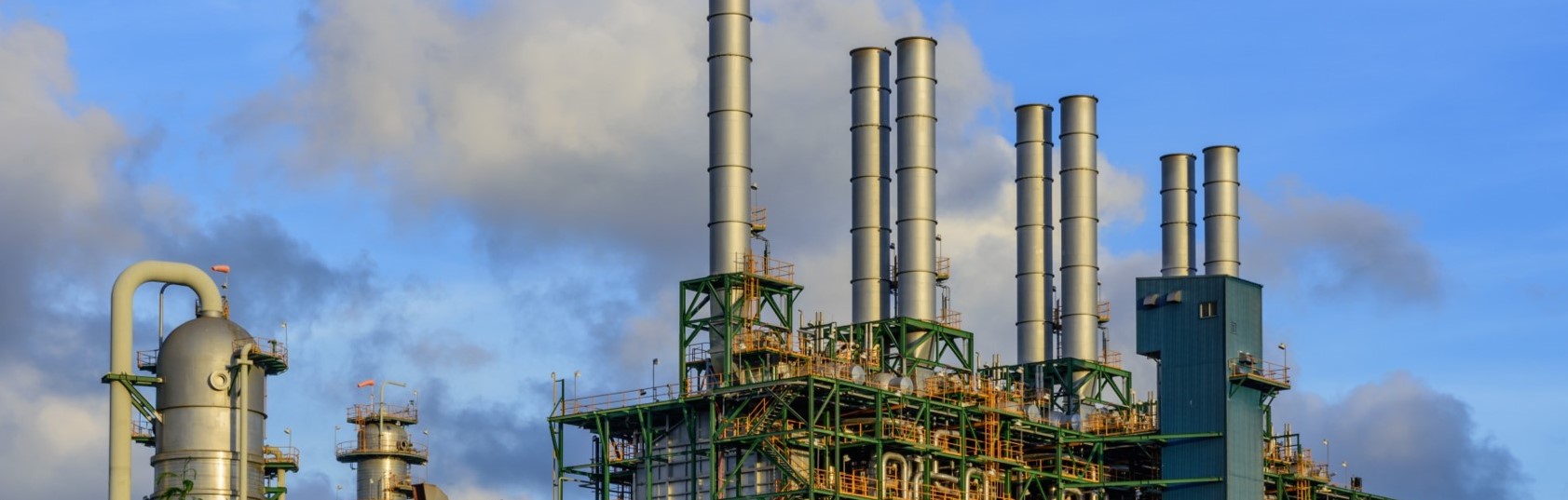
La formación de coque interna en los reactores de craqueo al vapor tubulares de las unidades de etileno tienen una influencia importante en la viabilidad económica y la eficiencia energética del proceso. Cuando el coque se forma dentro de las bobinas de craqueo al vapor, da como resultado una caída de presión más alta, lo que modifica la duración de funcionamiento operativo y la selectividad de la unidad. Debido a la formación de coque, la temperatura del metal del tubo (TMT) aumenta con el tiempo, lo que finalmente requiere la desconexión del horno para la "descoquización". El resultado es la pérdida de la producción y el aumento de la utilización de energía y los costos de mantenimiento.
Muchas iniciativas se han llevado a cabo en los últimos años para desarrollar tecnologías para reducir la formación de coque. Veolia ha desarrollado un nuevo recubrimiento catalítico patentado, llamado YieldUp, que tiene una estructura química única capaz de convertir el coque en óxidos de carbono al contacto.
El innovador recubrimiento YieldUp se aplicó a los nuevos tubos de horno instalados en una unidad europea de craqueo al vapor de etileno a 30 T/h, que utilizaba diferentes tipos de materias primas (p. ej., nafta, LPG y butano), para determinar su eficiencia y durabilidad. Los tubos recubiertos se utilizaron durante un período de 36 meses para determinar si podían reducir la frecuencia de descoquización, que anteriormente se realizaba cada 40 días con tubos no recubiertos.
Figura 1: tubo de horno recubierto YieldUp
YieldUp es un recubrimiento catalítico patentado desarrollado por nuestro Centro de Investigación y Desarrollo.
El recubrimiento pasiva los sitios catalíticamente activos de la aleación del reactor, y reduce, de esta manera, la acumulación del depósito de coque catalítico. Impulsa la conversión del coque depositado en CO2 e hidrógeno a través de la gasificación, mediante la reacción de vapor a alta temperatura.
Las nuevas bobinas instaladas en la unidad de craqueo europea de etileno fueron recubiertas con una capa de 25 μm de YieldUp, que luego se sinterizaron en la superficie interna de la bobina. Luego, las bobinas se armaron, soldaron e instalaron en la unidad de craqueo al vapor.
Durante la operación con los tubos recientemente recubiertos, el horno procesó varias materias primas. Esto permitió controlar la formación de depósitos de coque que se producían en distintas condiciones operativas.
Resultado
El indicador clave de rendimiento de la efectividad y el rendimiento del recubrimiento consistió en el perfil de temperatura del metal del tubo (TMT) durante el funcionamiento (Figura 2).
Figura 2: control de la TMT del horno con tubos recubiertos
La TMT inicial durante el reinicio, después de la descoquización, fue sistemáticamente más baja por un rango de 10-20 °C (18-36 °F). Según lo previsto, la curva de TMT durante el funcionamiento completo fue más aplanada para un horno sin recubrimiento, lo que generó una extensión del tiempo de funcionamiento del horno hasta que se alcanzó la TMT máxima de 1120 °C (2250 °F).
La eficacia de YieldUp puede observarse después de cada ciclo de descoquización como picos de CO2, lo que indican la gasificación del coque catalítico y la reducción de la formación de depósitos en los tubos.
También se llevaron a cabo análisis metalúrgicos en los tubos tratados después de 9 meses de operación y varios ciclos de descoquización, lo que confirma la presencia del recubrimiento y, por lo tanto, su durabilidad después de varias ejecuciones.
Durante los 36 meses de operación con los tubos recubiertos con YieldUp, la frecuencia de descoquización del horno se redujo a la mitad, duplicando efectivamente los períodos de funcionamiento desde un punto de partida de menos de 40 días hasta un promedio de casi 80 días (Figura 3).
Figura 3: período de funcionamiento entre la descoquización del horno europeo
Los ahorros de combustible asociados con la creciente eficiencia de transferencia de calor y la reducción de la frecuencia de descoquización se calcularon en ~3%, lo que se traduce en un ahorro aproximado de 500,000 € por año y en la eliminación de ~3000 T/año de CO2. La reducción de la frecuencia de descoquización también proporciona mayor tiempo de funcionamiento, aumentando así la productividad de la planta en un 3% estimado. Asimismo, se espera que se extienda la vida útil de la bobina como resultado de la menor deformación y carburización, lo que representa ventajas operativas significativas.