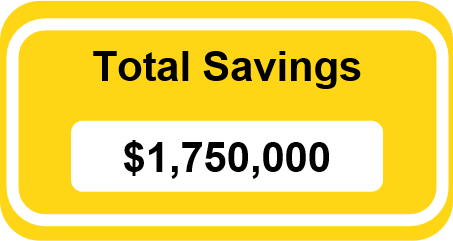
Desafío
Una planta de procesamiento químico líder en el sector que produce olefinas en América del Norte opera dos intercambiadores verticales de carcasa y tubos (A y B) que utilizan agua de alimentación de la caldera y condensado de vapor para eliminar el calor del proceso. Dado que estas unidades son propensas a la incrustación de partículas de hierro en suspensión, se realizan pruebas periódicas con filtros Millipore para confirmar que la contaminación por hierro se mantenga en niveles bajos en los afluentes y efluentes de las unidades.
Históricamente, ambos intercambiadores siempre arrojaron buenos resultados de hierro, por debajo de 50 ppb como Fe, que el representante técnico de Veolia mide mensualmente con Millipores. Después de una interrupción, a pesar de que se puso en línea un intercambiador recién limpiado, los niveles de hierro se mantuvieron altos (figura 1, línea azul), por lo que se cambiaron después de un año de operación y se inspeccionaron.
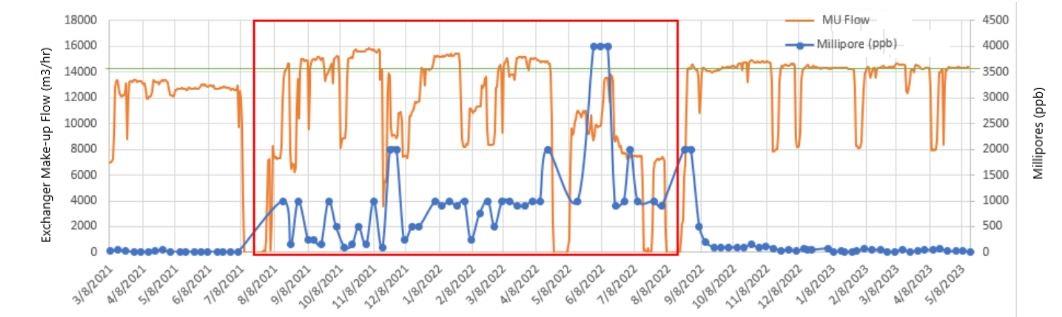
Figura 1: las pruebas de hierro Millipore mostraron resultados altos a lo largo de 2021-2022 (línea azul) a medida que las cargas de vapor iban alcanzando el 120 a 125% del diseño (línea naranja)
Solución
Se recolectaron muestras de tubos de las secciones media e inferior, y se realizaron análisis metalúrgicos en el Laboratorio Analítico de Veolia en Tomball, Texas, donde se observaron ranuras alargadas y picaduras en el metal. Veolia también revisó los cambios en las prácticas operativas y auditó el programa de tratamiento de agua para garantizar que se siguieran las mejores prácticas. Se realizó un estudio completo para comprender el funcionamiento interno del recipiente.
Las características de diseño del recipiente presentaron desafíos especiales en el lado del agua:
1) El recipiente no tiene tambor de vapor integrado, sino que utiliza deflectores. Por la falta de un tambor de vapor integrado, había una interfaz interna líquido/vapor con un espacio de descarga de vapor restringido, lo que hacía que esta área fuera propensa a la corrosión y la deposición. El recipiente también es más sensible a los cambios en el nivel del agua, lo que provoca altas tasas de purga, especialmente purgas intermitentes, que pueden interrumpir la circulación interna y causar alarmas de bajo nivel de agua.
2) Mientras que las calderas convencionales tienen agua de alimentación que ingresa en la parte superior de la unidad, en esta caldera el agua de alimentación ingresa en la parte inferior y justo a contracorriente de una curva, lo que provoca un cambio direccional en la circulación del agua. El agua de alimentación de la caldera que ingresa en esta ubicación, más fría, puede haber causado problemas de temperatura y circulación.
3) Debido a la presencia de deflectores, múltiples giros de 180° en la ruta de circulación interna del agua hacen que el intercambiador sea más propenso a la deposición de partículas de óxido de hierro. Además, si se opera por encima de las cargas de vapor de diseño, esta geometría puede ser propensa a la corrosión por flujo acelerado (FAC) y/o a la corrosión por erosión.
4) Los puntos de purga continua y de muestreo de agua de caldera se encuentran cerca de la parte inferior de la unidad. La práctica recomendada es recolectar agua de purgas continuas justo debajo de la línea de flotación para que se pueda tomar muestras más concentradas y representativas. El agua recolectada en el fondo de la unidad mostrará altas cantidades de sólidos sedimentados que pueden no ser representativos de la condición general del agua.
El análisis metalúrgico de las muestras de tubos mostró evidencia de ranuras y picaduras alargadas en el fondo de los tubos, pero ningún signos de corrosión acelerada por flujo (FAC). Esto podría indicar que cuando el intercambiador se opera por encima del 110% del diseño, existen condiciones en el recipiente que causan pérdida de hierro y/o corrosión, sin estar relacionadas con FAC. Esto podría deberse a una condición anormal de ebullición a alta velocidad, o a la evaporación a sequedad que deja que se depositen sales corrosivas. En estos casos, se sugirió que el cambio del material de la carcasa y el tubo por una aleación de mayor grado podría proporcionar una protección adicional si las cargas de vapor superan el 110% del diseño.
Resultado
Después de revisar los datos operativos, se observó una fuerte correlación entre los resultados altos de hierro y las cargas de vapor que alcanzan un 120 a 125% por encima del diseño. En las operaciones anteriores, las cargas máximas de vapor habían llegado un 110 a 115 % por encima del diseño (figura 1, línea naranja). El intercambiador se puso en funcionamiento en junio, pero las condiciones inestables de la planta durante el otoño proporcionaron resultados poco fiables con los Millipore durante este período. Con la estabilización de la operación de la planta después de septiembre y con la prueba iniciada para mantener las cargas de vapor en el intercambiador por debajo del 120% del diseño, se observó que los niveles de hierro se iban estabilizando, hasta que finalmente disminuyeron. Millipore indica un nivel más alto de hierro obtenido de la muestra, pero no identifica la fuente de la contaminación por hierro.
Para garantizar que los intercambiadores de calor puestos en funcionamiento después de las interrupciones estuvieran en condiciones óptimas de arranque, la planta desarrolló procedimientos para la limpieza y pasivación fuera de línea.
Tras los cambios operativos realizados en los intercambiadores, donde las cargas de vapor ahora se controlan hasta un máximo del 110% del diseño, los Millipores han vuelto a la normalidad y se continúa haciendo un seguimiento. Dado que una falla del intercambiador habría provocado una interrupción mínima de 3 días con un costo adicional de reemplazo o reentubado del intercambiador, los ahorros se estimaron en $1,750,000.
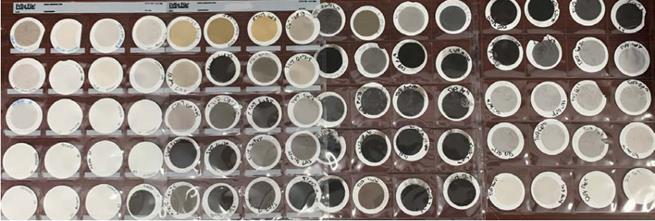
Figura 2: resultados de Millipore que muestran una tendencia creciente del hierro y una disminución de los niveles de hierro después de reducir la carga por debajo del 120%